表面処理加工サービス
表面処理加工の形態
表面処理加工とは、材料表面に何らかの方法で処理加工を施し、表面特性を変化させる、または新たな特性や機能を付加することをいいます。表面処理を施した材料の表面には変化が生じ、この変化(加工現象)は5つの形態に分類することができます。
また、表面処理加工には、下記のような付加加工だけでなく、洗浄・研磨・エッチングといった表面処理なども存在します。
①.組成は変化させず、表面のみの特性改善を施すもの
たとえば、高周波焼き入れの場合、表面の組成自体は全く変化させません。しかし、急速加熱冷却されると表面が硬化し、耐摩耗性の向上といったメリットが生まれます。
②.他の元素が染み込み、改質されるもの
たとえば、窒化処理の場合、窒素が拡散浸透することで耐摩耗性や耐疲労性の向上といったメリットが生まれます。
③.化学反応によって改質されるもの
たとえば、アルミニウムの陽極酸化の場合、酸化物層を生成することで耐摩耗性や耐食性の向上といったメリットが生まれます。
④.表面に基材と全く異なる処理層を形成するもの
このカテゴリーに該当する表面処理加工は、めっき塗装、ライニングなど多数存在します。
⑤.表面に基材と全く異なる処理層を形成し、基材との境界において元素の拡散を生じているもの
たとえば、溶融亜鉛メッキがこのカテゴリーに該当します。
表面処理の方法を採用するポイント
表面処理加工を施す場合、既存の製品や部品にそのまま単純に追加採用といった形で表面処理加工できるケースが多いのですが、それ以外に、製品や部品を構成している材料を変更しなければならないもの、寸法や形状を変更しなければならないもの、前熱処理や後熱処理など作業工程から変更しなければならないもの等、そのまま単純に追加採用といった形で加工するのではなく、都度考えながら表面処理加工方法を採用しなければならないケースも少なくありません。たとえば、表面処理を採用することでもたらされるメリットがいくら素晴らしくても、適用製品や部品との相性が悪い、もしくは使用環境や使用条件にマッチングしていないという場合、その効果は十分に発揮されません。(図①参照)不適切な表面処理方法を採用したことにより早期損傷してしまう危険性もあるのです。このようなことを鑑み、表面処理方法を採用する際には、以下の6つのポイントに留意する必要があります。
- ① 基材(製品や部品を構成している材料)と採用したい表面処理との相性はどうなのか
- ②.採用したい表面処理の処理工程中に基材の劣化(加熱に伴う軟化、ぜい化、寸法変化、変形等)が起こらないか
- ③.製品や部品の表面状態(表面粗さ、表面の変質や汚染等)は、採用したい表面処理加工に適しているか
- ④.製品や部品の形状(表面処理必須箇所が細孔内面や隙間側面である等)は、採用したい表面処理加工に適しているか
- ⑤.採用したい表面処理加工は、その製品や部品の使用環境、並びに使用条件に適合しているか
- ⑥.表面処理加工の採用によって得られる効果が、コスト的に過剰な品質改善になっていないか
図① 主な表面処理の特性
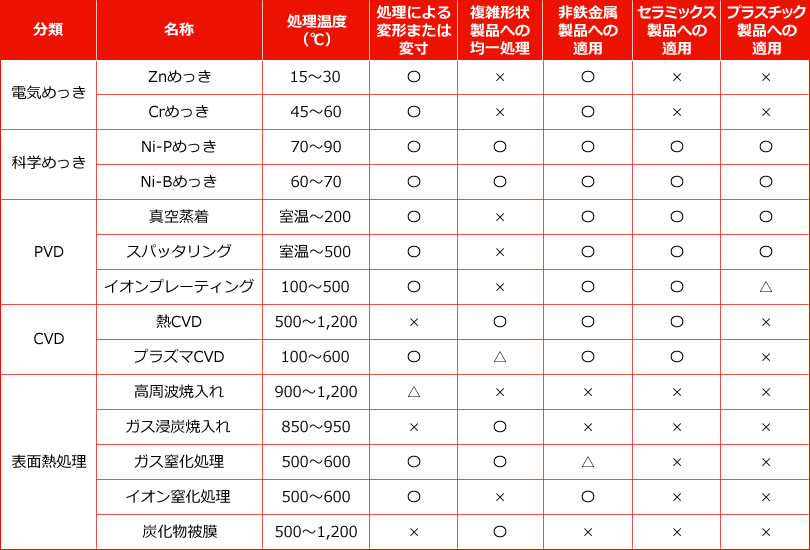
腐食や摩擦、耐疲労性や耐熱性に対する表面処理の採用
①.金属製品に発生する腐食現象
表面処理の最も重要な採用目的は、金属製品の湿式腐食(湿食)に対する防錆・防食といっても過言ではありません。湿食現象は、次の5つに分類することができます。
Ⅰ.全面腐食
均一腐食と呼ばれているもので、金属表面が全面的に一様に腐食していく現象です。対策としては比較的簡単で、使用環境に適した材料の選定、塗装などの表面処理の採用、減肉速度に応じた寸法の設計などが挙げられます。
Ⅱ.ガルバニック腐食(異種金属接触腐食)
鉄と亜鉛、銅とニッケルといった異種金属が水溶液中で接触することによって、卑な金属(自然電位の低い金属)の腐食が促進され、貴な金属(自然電位の高い金属)の腐食が抑制される現象をいいます。めっき被膜にピンホールがあると、空気中の水分の結露によって同様な現象が起きます。
Ⅲ.孔食
孔食とは、表面の局部に集中して生じる腐食のひとつで、ピット状に腐食し、それらの周辺には腐食は観察されないのが特徴です。孔食の発生原因として、金属表面の不均一組織、表面保護膜の局部的な破壊、といったものが挙げられます。
Ⅳ.粒界腐食
金属の結晶粒界は不純物の偏析や化合物の析出を伴うことが多いので、結晶粒界に沿って局部的に腐食が進行する傾向があります。特によく起こる粒界腐食に、オーステナイト系ステンレス鋼のクロム炭化物の析出による腐食があります。
Ⅴ.すきま腐食
金属製品において、ボルト締結箇所や溶接箇所など金属板同士の継ぎ目部分(すきま)に発生する腐食がすきま腐食です。すきま内部は外部周辺よりも溶存酸素の供給が希薄になるため、酸素濃淡電池が形成されやすい傾向にあります。防止対策としては、なるべくすきまが存在しないような締結方法や接合方法を採用することが挙げられます。
②.金属皮膜による防錆・防食
金属材料の防錆・防食方法には多くの方法がありますが、そのなかでも金属皮膜は良く使われる方法です。金属皮膜は、被膜が基材よりも卑な金属の場合と貴な金属の場合とで防食原理が異なります。
Ⅰ.被膜が卑な金属の場合
建造物などに主に使用されている溶融亜鉛めっきや亜鉛溶射、ボルトなどへの亜鉛めっきはわかりやすい事例です。特に、溶融亜鉛めっきは鋼の防錆を目的として多く利用され、他の表面処理に比べ防錆期間が長く経済的にも有効な表面処理です。また、処理物の形状や大きさの制約を受けにくいことから、小物から大物部品まで幅広い分野で使用されています。この防食原理は、鉄よりも卑な金属である亜鉛がアノードによって溶出することで下地である鋼を腐食から守るというものです。この防食方法のことを犠牲防食といいます。ガルバニック腐食を逆に防食に利用したものと考えられ、卑な金属が溶解してしまうまでその効果が保たれるので、基材を長期間腐食から防ぐことができます。
Ⅱ.被膜が貴な金属の場合
被膜としては、ニッケル・スズ・金などがあります。湿式環境下では被膜の方が基材である鉄よりも貴なので、被膜から基材に向かって電流が流れるため、ピンホールなどのめっき欠陥箇所から基材の腐食が進行すると考えられています。つまり、これらの被膜は、乾式環境下における装飾などを主な目的とするのであれば非常に有効といえますが、空気の存在する湿潤環境下での防食効果は期待できないといえます。
③.様々な摩耗
どのような製品においても、使用中に摩擦を伴う箇所では、必ず摩耗が発生するため、その対策として様々な表面硬化処理がなされます。摩擦の原因によって摩耗を分類すると、一般的に、凝着摩耗・アブレシブ摩耗・防食摩耗・疲労摩耗に分類されます。ただ、実際ではこのように明確に分類することが難しく、それぞれの分類にまたがる摩耗であることが多いです。
Ⅰ.凝着摩耗
すべり摩擦面に発生する摩耗で、無潤滑状態における相手材の融着が主な原因となります。潤滑環境であっても油膜が無くなり、境界潤滑状態になれば同じような現象を生じることから、この摩耗を防ぐためには、しっかりとした潤滑環境を構築することに注意しなければなりません。
Ⅱ.アブレシブ摩耗
硬い粒子によって表面が削られて生じる摩耗のことをいいます。硬い粒子としては、お互いのバリや突起、外部からの異物混入などが考えられます。削り取られることが原因となるので、別名、切削摩耗・引っかき摩耗、スクラッチングともいわれます。
Ⅲ.腐食摩耗
腐食環境(反応ガス、化学薬品等)で使用した場合に、反応生成物が生じ、それが剥がれてしまうことで摩耗する摩耗のことを腐食摩耗と呼びます。
Ⅳ.疲労摩耗
お互いの繰り返し接触により生じる表面損傷(亀裂・剥離等)のことで、種類としては、ピッチング・フレーキング・スポーリング等があります。
④.耐疲労性
物体が繰り返し応力を受けた際に、その応力が物体の持つ引張強さよりも小さい応力であっても、徐々に亀裂が発生・進展することで最終的に破壊されてしまうことがあります。製品や部品の破壊の原因の多くがこの疲労によるものです。疲労強度は静的な引張強さに依存し、基本的には硬さを高めることで強くすることができます。また、初期段階での亀裂はほぼ表面に発生するので、表面硬化処理をすることで大きな耐疲労性をもたらすことができます。具体的には、高周波焼入れなどの表面焼入れ、浸炭焼入れなどの熱拡散処理、ショットピーニングなどが、疲労強度向上を目的に適用されています。焼入れやショットピーニングはいずれも表面硬化による耐摩耗性向上にも寄与しますが、なにより表面に形成される大きな圧縮応力が疲労強度を大幅に高めます。自動車用歯車のように、浸炭焼入れした後にショットピーニングを行うなどの複合的な適用例もあります。
また疲労強度は、製品の形状や表面粗さなど、材料による影響や応力が常に一定ではないことを考えると、外的な要因が少なからずとも影響を与えていることを考慮しなければなりません。
⑤.耐熱性
耐熱性の付加のみを目的とした表面処理はあまり多くなく、主に耐摩耗性といった他の特性付加を主な目的とした表面処理の副次的な効果として、付加されます。また、表面処理の分野や使用状況によって、求められる耐熱性の程度は変わります。例えば、自動車などのエンジン部品であるピストンヘッドやシリンダヘッド、さらにはジェットエンジンや発電用ガスタービンの部品などは耐熱性が強く求められます。これらに対応する表面処理としては、薄膜や金属膜では効果が期待できないため、厚膜を得意とする溶射によるセラミックコーティングが多く適用されます。塗装分野には、オートバイや自動車のマフラー、エンジンカバー、ボイラー熱交換器を対象とした塗料が存在します。また、切削工具においては使用中に刃先がかなりの高温になるため、PVDによるチタン系の硬質膜が適用されるケースが増えてきています。
コーティング(非金属被膜処理)
①.塗装
塗装の目的の多くは、防食と装飾です。塗装の大きなメリットとしては、常温で施工できること、塗装対象の大きさや形状などにほとんど影響を受けないことが挙げられます。
Ⅰ.塗料の分類
塗料は、樹脂を主原料として、顔料、溶剤、使用目的にあった添加剤から構成されています。塗料の分類には、主原料である樹脂の種類によるもの、使用用途によるもの、塗装方法によるものなど多くの分類法があります。一般的には、用途別もしくは樹脂別に分類されることが多いです。(図②参照)
図② JISにみる塗料の目的別種類
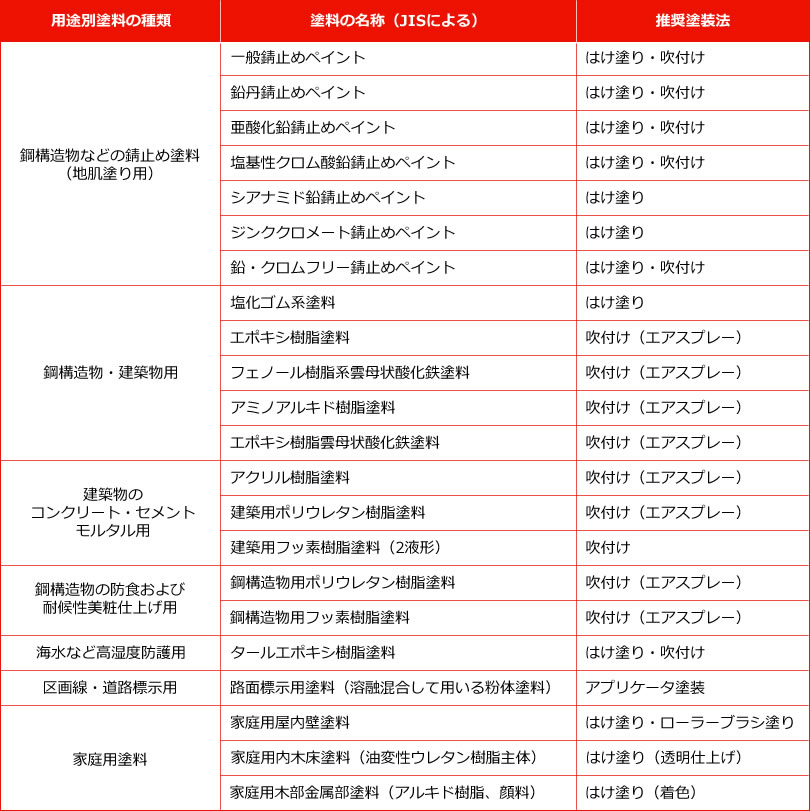
Ⅱ.溶剤塗装
溶剤塗装は最も一般的な塗装方法であり、小物から大型構造物まで広範囲にわたる分野で使用されています。その塗装方法は、はけ塗り・ローラー塗装といった一般的なものから、大掛かりな機械や装置を使ったものまで多岐にわたります。
Ⅲ.粉体塗装
粉体塗装は、粉末状の塗料を用いて塗装するもので、最大の特徴は水や有機溶剤を使用する必要がない所です。粉体塗装法には、流動浸漬塗装と静電粉末塗装があります。
- 流動浸漬塗装
粉末塗料の容器に底部から吹き込んだ圧縮空気を使うことで塗料を流動させ、容器の中に塗装したい製品を浸漬したものです。 - 静電粉体塗装
スプレーガンを用いて塗装するもので、静電気を利用します。つまり、スプレーガンの中で粉末塗料に高電圧を帯電させ、逆極性に設定した塗装製品に圧縮空気を用いて吹付けます。
②.ライニング
ライニングは、内張りともいわれ、防錆・防食を目的として、化学工業などの多くの分野で利用されています。種類としては、ゴムライニング・樹脂ライニング・グラス(ガラス)ライニングがあります。
Ⅰ.ゴムライニング
通常ゴムライニングは、未加硫ゴムを母材に接着し、蒸気釜で加硫して施工します。製作可能サイズは蒸気釜の大きさに規定されます。主にタンクや各種ロール、ホッパー、配管などの表面に施工し利用されています。
Ⅱ.樹脂ライニング
ライニング材として塗料用樹脂を使います。厚塗り塗装として位置づけられることが多く、シート状の樹脂を接着剤で貼り付けるシートライニング、液状の樹脂を使用する液状ライニング、紛体樹脂を塗布して加熱溶融させて被膜にする紛体ライニングがあります。
Ⅲ.グラス(ガラス)ライニング
鋼製品にガラスを溶融コーティングするものです。多くの目的は、耐食性を付加することで、各種貯蔵タンクの内面保護に良く利用されています。装飾品として有名な「七宝焼き」もこのコーティング方法で製作されています。